Diesel Fuel Maintenance & Load Bank Testing in Utah
Generators rely on having clean diesel fuel for efficient and reliable operation. The ultra fine tolerances and high
fuel injection pressures of today’s diesel fuel systems create extreme sensitivity to any fuel quality problems or
contamination. Fuel quality problems and contaminants comes from a variety of sources which if left unaddressed it can lead to an assortment of problems.
Contamination Type: Water
Cause
Poor fuel handling and transfer
processes.
Leaking fuel tanks.
Condensation within the fuel tank.
Poor quality fuel delivery.
Leaking fuel tanks.
Condensation within the fuel tank.
Poor quality fuel delivery.
Effect
Engine and fuel system damage.
Corrosion.
Fuel oxidation.
Growth of diesel bug.
Corrosion.
Fuel oxidation.
Growth of diesel bug.
Contamination Type: Biogrowth
Cause
Grows as a result of water contamination.
Effect
Blocked engine filters & fuel
components.
Corrosion of fuel tanks.
Corrosion of fuel tanks.
Contamination Type: Asphaltines
Cause
Naturally occurring in fuel.
Increases with heat & mechanical stress to fuel.
Increases with heat & mechanical stress to fuel.
Effect
Blocked engine filters.
Contamination Type: Gums, Resins & Acids
Cause
Fuel oxidation, accelerated by water
content.
Effect
Fuel oxidation, accelerated by water
content.
Contamination Type: Fuel oxidation, accelerated
by water content.
Cause
Poor fuel quality, poor fuel handling,
corroding fuel tanks.
Effect
Filter blockage and fuel systems wear.
KEYS TO PREVENTING COSTLY DIESEL FUEL RELATED DOWNTIME.
1. Keep fuel tanks full to reduce condensation buildup.
2. Only use quality fuel that has been properly treated during each fueling.
3. Inspect the fuel and fuel tank at least semi-annually for water and other visual contamination or degradation.
4. Change fuel filters annually or every 250 hours of operation which ever comes first.
2. Only use quality fuel that has been properly treated during each fueling.
3. Inspect the fuel and fuel tank at least semi-annually for water and other visual contamination or degradation.
4. Change fuel filters annually or every 250 hours of operation which ever comes first.
5. Annually sample and lab test fuel from large tanks, extremely critical tanks, and tanks that aren’t completely
cycled annually.
6. Polish fuel on an as needed routine bases.
7. Treat fuel after polishing depending on conditional needs and lab test results.
6. Polish fuel on an as needed routine bases.
7. Treat fuel after polishing depending on conditional needs and lab test results.
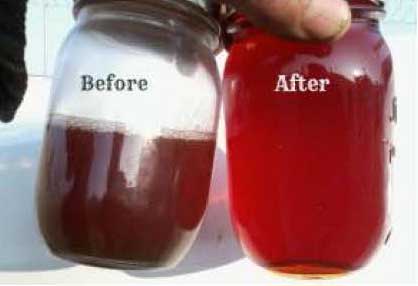
Precision Power’s fuel polishing system removes contaminants
from the fuel and reconditions fuel with a five stage centrifugal
filtration process. This fuel reconditioning process will clean and
restore the fuel to a clear and bright condition – saving you fuel
costs and ensuring the generator’s engine will operate efficiently
at a moment’s notice.
Proper fuel maintenance is important and often overlooked by many. With regular planned maintenance that includes a routine fuel polishing process you can combat potential problems.
Proper fuel maintenance is important and often overlooked by many. With regular planned maintenance that includes a routine fuel polishing process you can combat potential problems.
STANDBY GENERATORS
Emergency standby generators are usually never run under full load. They typically run
under no load during exercising and often under 50% of their nameplate rating during
power outages. As a result, generators never reach their optimal operating temperature.
Continued operation at these reduced load levels can result in diminished performance or
worse complete failure because of the following conditions:
- Collection of unburned combustion products deposited on exhaust valves, turbochargers, and
manifolds.
- Poor cylinder wall lubrication or ring seating, cylinder liner glazing, and excessive
lubricating oil consumption.
- Moisture accumulation in generator windings.
WHY PERFORM LOAD BANK TESTING?
- Weekly exercising introduces no load to the generator.
- Confirms proper engine performance under a load.
- Dries out moisture build-up on internal parts.
- Cleans out “wet stacking” (unburned fuel deposits)
- Assures that standby power is available when needed.
- It is a JCAHO requirement for healthcare facilities.
- It is a NPFA requirement for many facilities.
- Confirms proper engine performance under a load.
- Dries out moisture build-up on internal parts.
- Cleans out “wet stacking” (unburned fuel deposits)
- Assures that standby power is available when needed.
- It is a JCAHO requirement for healthcare facilities.
- It is a NPFA requirement for many facilities.
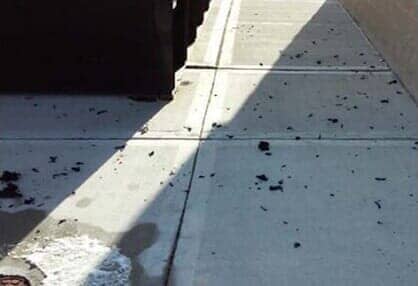
LOAD BANK TESTING INCREASES PERFORMANCE AND RELIABILITY
Critical application of standby power such as medical care, public safety, communications,
manufacturing, government operations, and data transmission just to name a few has created
the need to maximize the performance and reliability of standby generators. Based on our
experience of maintaining thousands of generator sets Precision Power, Inc. recommends an
annual four hour load bank test to minimize performance and reliability.
BENEFITS OF LOAD BANK TESTING
- The generator is brought to peak operating temperature for an extended period.
- By-products are combusted. (unburned fuel deposits)
- Piston rings and other parts seat properly.
- Moisture evaporates from the generator and associated components.
- It verifies overall reliability to perform in an emergency power situation. (Horse power, voltage and frequency stability)
- It removes some of the risk of total power loss.
- By-products are combusted. (unburned fuel deposits)
- Piston rings and other parts seat properly.
- Moisture evaporates from the generator and associated components.
- It verifies overall reliability to perform in an emergency power situation. (Horse power, voltage and frequency stability)
- It removes some of the risk of total power loss.